Dr. Mohammad Hadi Hafezi

-
Fatigue Crack Growth Models: The research explores fatigue crack growth models that incorporate elastic-plastic stress-strain histories at the crack tip region and strain-life damage models.
-
UniGrow Model: The UniGrow model is specifically designed to fit within this class of fatigue crack propagation models. It takes into account residual stresses at the crack tip, which play a crucial role in assessing the actual crack driving force.
-
Importance of Residual Stresses: Residual stresses are significant in these models as they consider mean stress and loading sequential effects. They provide valuable insights into crack propagation behavior.
-
Performance Assessment: The research assesses the performance of the UniGrow model by utilizing available experimental constant amplitude crack propagation data obtained from various metallic materials found in representative Portuguese bridges.
-
Predicting Fatigue Crack Growth: The UniGrow model offers a means to predict fatigue crack growth accurately. However, key issues related to residual stress computation are discussed, highlighting important considerations in fatigue crack growth prediction using this model.
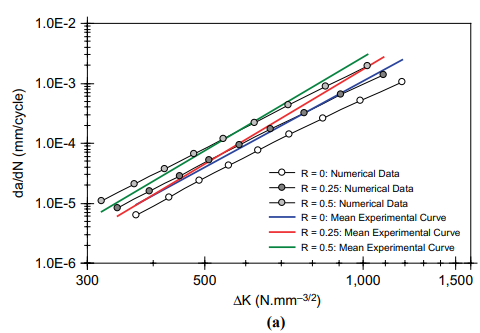

Software Solution
Advancements in Fatigue Crack Growth Predictions for Metallic Structures: A Strain-Based Approach
This analytical article delves into significant research efforts focused on investigating the strain-life and fatigue of metallic-riveted bridges in Portugal. The study utilizes the UniGrow model, a residual-based fracture crack propagation model, to analyze fatigue behavior. By leveraging fatigue tests, strain-life data, and elastoplastic finite element analysis, the research proposes a strain-based approach for accurate predictions of fatigue crack propagation rates across various stress ratios. The study highlights the limitations of the original analytical approach, the Smith-Watson-Topper damage parameter, and emphasizes the consistent results achieved with the alternative elastoplastic finite element analysis, specifically the Coffin-Manson law. This proposed approach offers enhanced precision, reduced cost, and time efficiency, making it a valuable tool for predicting fatigue in metallic structures such as bridges and aircraft, ultimately contributing to improved safety and mitigating catastrophic structural failures.
Introduction:
In the realm of structural engineering, fatigue-induced failure poses a significant challenge, particularly for metallic structures such as bridges. Fatigue, characterized by the degradation of metal strength due to cyclic stress, leading to crack formation and potential catastrophic collapse, necessitates accurate predictions for effective maintenance and safety protocols. This article investigates advancements in fatigue crack growth predictions, specifically focusing on strain-based approaches and the application of the UniGrow model.
Fatigue Analysis with the UniGrow Model:
The UniGrow model, a residual-based fracture crack propagation model, serves as the basis for fatigue analysis in metallic-riveted bridges. By considering the residual stress at the crack top, this model enables a comprehensive assessment of fatigue behavior. The aim of the research is to evaluate the performance of the UniGrow model and propose improvements for more accurate fatigue predictions.
Development of Fatigue Damage Model:
To assess the performance of the UniGrow model, fatigue tests on smooth metal specimens and strain-life data are conducted. These tests provide essential input for the development and proposal of a fatigue damage model. The collected data is employed to calculate predicted crack growth rates, which are subsequently validated by comparing them with experimentally obtained propagation data from standard compact tension specimens.
Challenges with the Analytical Approach:
The original analytical approach employed in the UniGrow model, utilizing the Smith-Watson-Topper damage parameter, exhibits inconsistencies in predicting fatigue crack growth rates. Notably, this approach tends to overestimate stress effects, particularly in cases where material samples demonstrate moderate stress sensitivity in crack propagation rates.
Adopting the Elastoplastic Finite Element Analysis:
To address the limitations of the original analytical approach, the research proposes the use of elastoplastic finite element analysis as an alternative. This advanced analysis method, employing the Coffin-Manson law, consistently produces accurate results in fatigue crack growth predictions. By considering the strain-based approach and utilizing finite element analysis, the proposed model offers enhanced precision and reliability.
Benefits and Implications:
The proposed strain-based approach using elastoplastic finite element analysis represents a significant advancement in predicting fatigue crack growth rates for metallic structures. Beyond the improved accuracy, this approach also presents cost and time advantages, making it a practical solution for assessing fatigue in structures such as bridges and aircraft. By enhancing prediction methods, the model contributes to increased safety and a reduced risk of catastrophic structural collapses.
Conclusion:
Through extensive research efforts, this study emphasizes the importance of strain-based approaches and advanced analysis methods in predicting fatigue crack growth rates for metallic structures. The proposed strain-based approach, employing elastoplastic finite element analysis, offers superior accuracy compared to the original analytical approach. This innovative model holds significant promise for accurately determining fatigue in metallic structures, thereby enhancing safety and mitigating potential structural failures.

Fatigue Crack Growth
Fracture Mechanics
Fatigue
Creep
Damage
-
Hafezi MH, Abdullah NN, Correia JF, De Jesus AM. An assessment of a strain-life approach for fatigue crack growth. International Journal of Structural Integrity. 2012 Nov 16;3(4):344-76.
-
Abdullah NN, Correia JF, De Jesus AM, Hafezi MH, Abdullah S. Assessment of fatigue crack growth data available for materials from Portuguese bridges based on UniGrow model. Procedia Engineering. 2011 Jan 1;10:971-6.